For those who are not experts in electricity, there is often a very common confusion:…
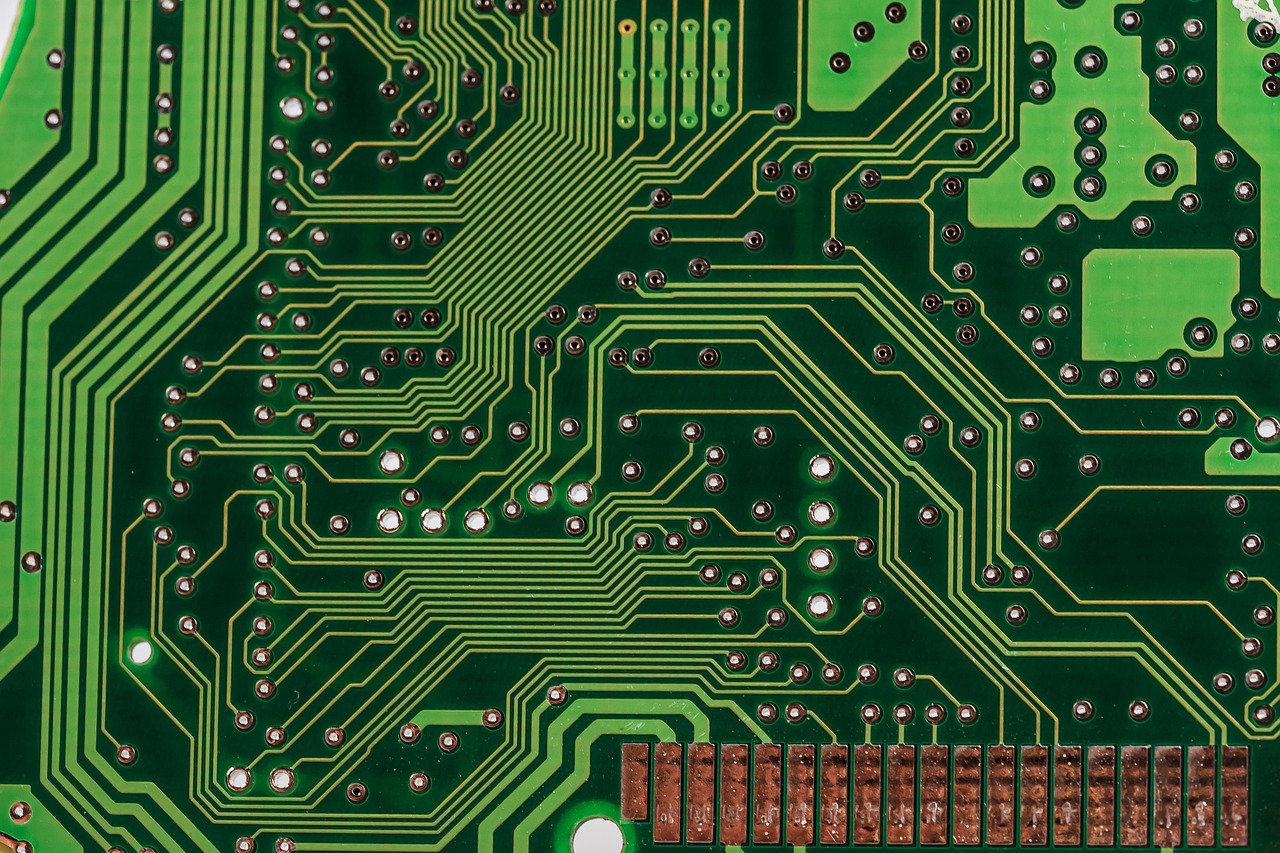
Discovering flexible electronic circuits
The technology of flexible electronic circuits is in full expansion. Also known by the acronym in English FPC (Flexible Printed Circuit), these components have multiple applications. Areas such as the healthcare sector, telecommunications or consumer electronics are just three examples of the areas of industry that incorporate this technology.
Thanks to printed electronics, it is possible to easily apply on flexible surfaces, circuits and other components. And this without affecting the flexibility of the substrate, which can be paper, fabric, plastic or metal. Given their advantages, FPCs are progressively replacing rigid electronic circuits. Next, the differences between both types of components are established.
Flexible vs. Rigid Electronic Circuits
A printed circuit board consists of a support or substrate on which various electronic components are installed. All of them are connected by means of conductive tracks made of copper sheets. The substrate for rigid electronic circuits prevents their deformation, which increases their useful life. They are the most widely used type of circuit.
Unlike rigid circuits, FPC components are placed on a flexible substrate. This is usually made of a polymer called polyimide, highly resistant to temperature and traction. The circuit tracks, or electrical conductors, are made of copper. Finally, a layer of flexible material is placed over the circuit for protection.
Among the advantages of flexible PCBs (Printed Circuit Boards) is their ability to deform. Thanks to this, they adapt to any space, no matter how irregular it may be. It is a facility that rigid circuits do not have. Another of their qualities is that they are lighter than rigid PCBs, given their shape and the material of the substrate.
Flexible electronic circuits are more durable than rigid ones, since they better withstand mechanical stress and vibrations. They also have high resistance to heat, electromagnetic interference and outdoor use. These characteristics are very important in teams in the healthcare sector and in the automotive industry.
Social healthcare sector: the revolution of flexible circuits
In 2030, it is expected that the turnover of electronic patches and textiles for the healthcare sector will exceed 2 billion dollars worldwide. This technology has only been possible thanks to the development of flexible electronic circuits.
Electronic skin patches adhere to the skin using an adhesive. They are used to monitor parameters such as heart rate, blood pressure or respiration. Given their characteristics, they are easy to use and increasingly have greater autonomy. For their part, the so-called “smart garments” allow monitoring of heart rate and other physiological indicators. They are more comfortable than patches and as aesthetic as normal garments.
Electrolomas is a specialist in the development and manufacture of flexible electronic circuits and wiring since 1997. Electromechanical assemblies are also carried out for various sectors related to health, such as dental, medical-aesthetic machinery, laboratory equipment and solutions for autonomous mobility. Likewise, the company’s professionals are specialized in the manufacture of surveillance and access systems. Contact the company if you want more information.