Rigid or conventional circuits
We design, manufacture and assemble electronic circuits using THT and SMT processes with automated soldering by reflow or wave oven.
Our electronics department can design a circuit according to the needs of the client/project, or adapt it to make it more functional, economical or have a size that suits the needs of the product or its industrialization.
Our circuits can be adapted to any sector, type of device, equipment or machine. We also carry out certain soldering or component placement manually, if the product requires it.
We carry out the optical inspection in an automated way, controlling 100% of the manufactured circuits.
Applications:
Manufacturing of electronic circuits: We carry out both the design and production of circuits using THT and SMD techniques.
Our electronics department can develop a circuit according to the needs of the client/project or adapt it to make it more functional, economical or have a size according to the need of the product or its industrialization.
The circuits we manufacture are applicable to any sector and type of device, equipment or machine.
We also carry out certain soldering or component placement by hand, if the product requires it.
Verification is automated, with 100% of the circuits we manufacture being controlled.
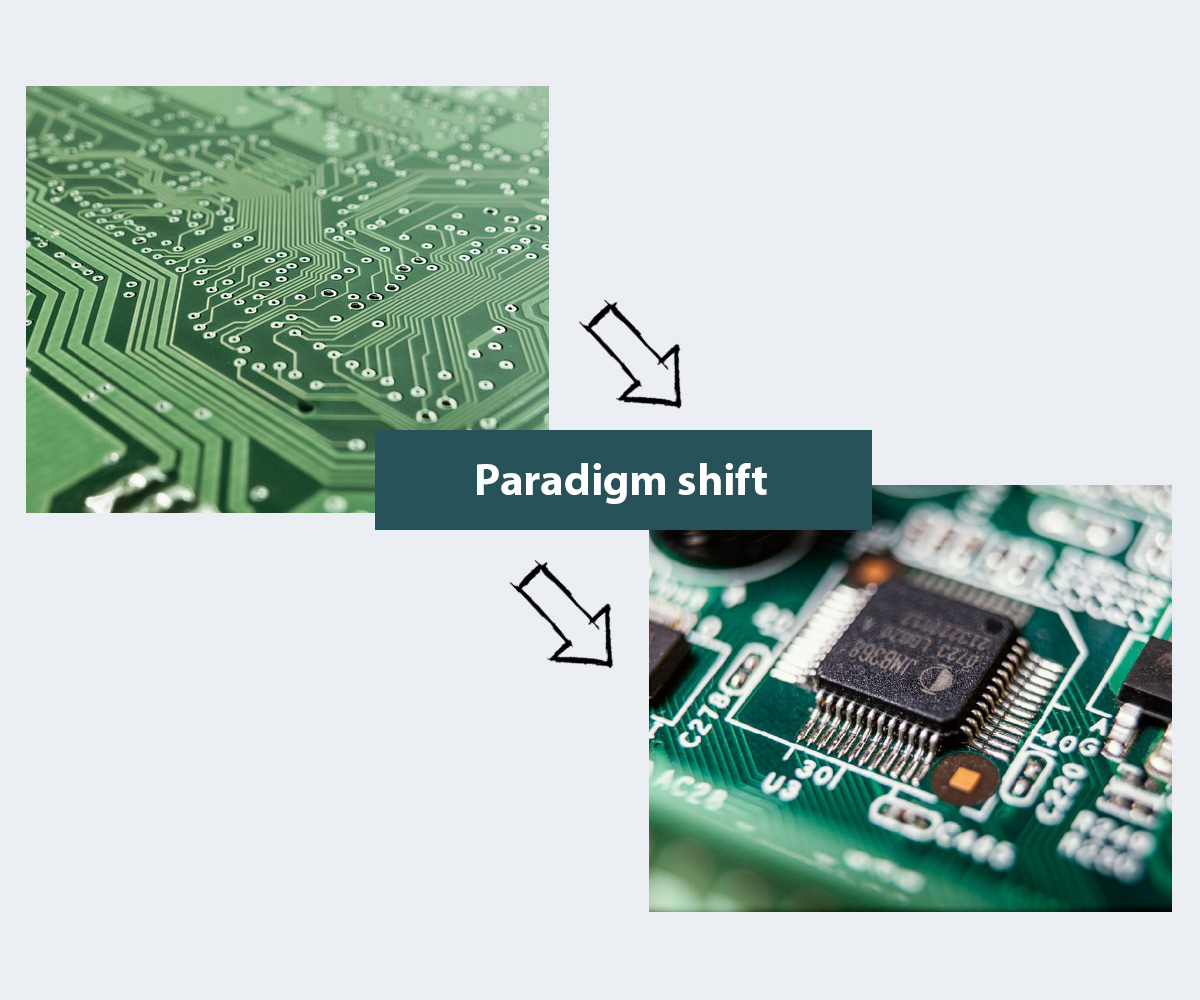
Flexible Printed Circuit Boards (FPCB)
Flexible circuits represent a paradigm shift: from a rigid circuit to a malleable one. A thin, easy-to-integrate type of circuit that can cover large areas and be mass-produced.
It has the built-in functionality of combining different devices on a single production substrate. And it offers new market opportunities thanks to its greater freedom of shape and size.
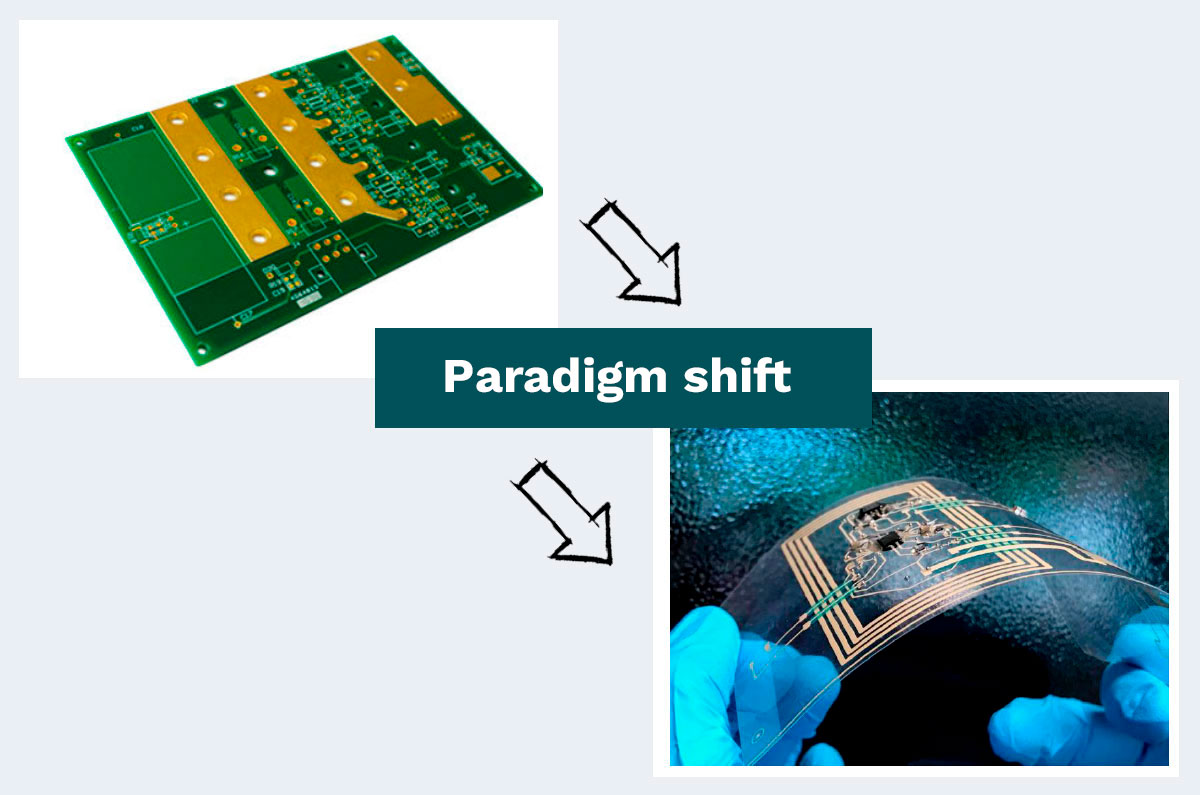
We have developed together with Eurecat the soldering of components in flexible circuits
Printed electronics is a technology that makes it possible to print electrical connections (tracks) directly on different substrates (plastic (PC, PET…), paper or textiles) electronic components, conductive tracks and circuits. In this way:
The flexibility of the substrates makes it possible to physically adapt the circuit and place it in areas that are not flat on the final part.
The flexible circuits can be used in In Mold Electronics (IME) processes, so that by thermoforming they can be shaped and injected with the resin that will form the final object, with the flexible electronic circuit being completely integrated into the final part.
The manufacturing process of our flexible circuits is:
We select the right substrate
We print the tracks and some components using conductive or dielectric ink.
In the case of hybrid technology, conductive adhesive is deposited to create an electrical connection between the leads and the SMD components
SMD components are placed using pick&place
The adhesive dots that will electrically bond the SMD components are heat cured
Structural glue is deposited to improve the mechanical bonding of the component to the circuit
The structural adhesive is then thermally or UV cured
At this point, the FPCBA is ready for further processes such as thermoforming, injection moulding which can give it non-flat shapes or for use in flexible textile wearables
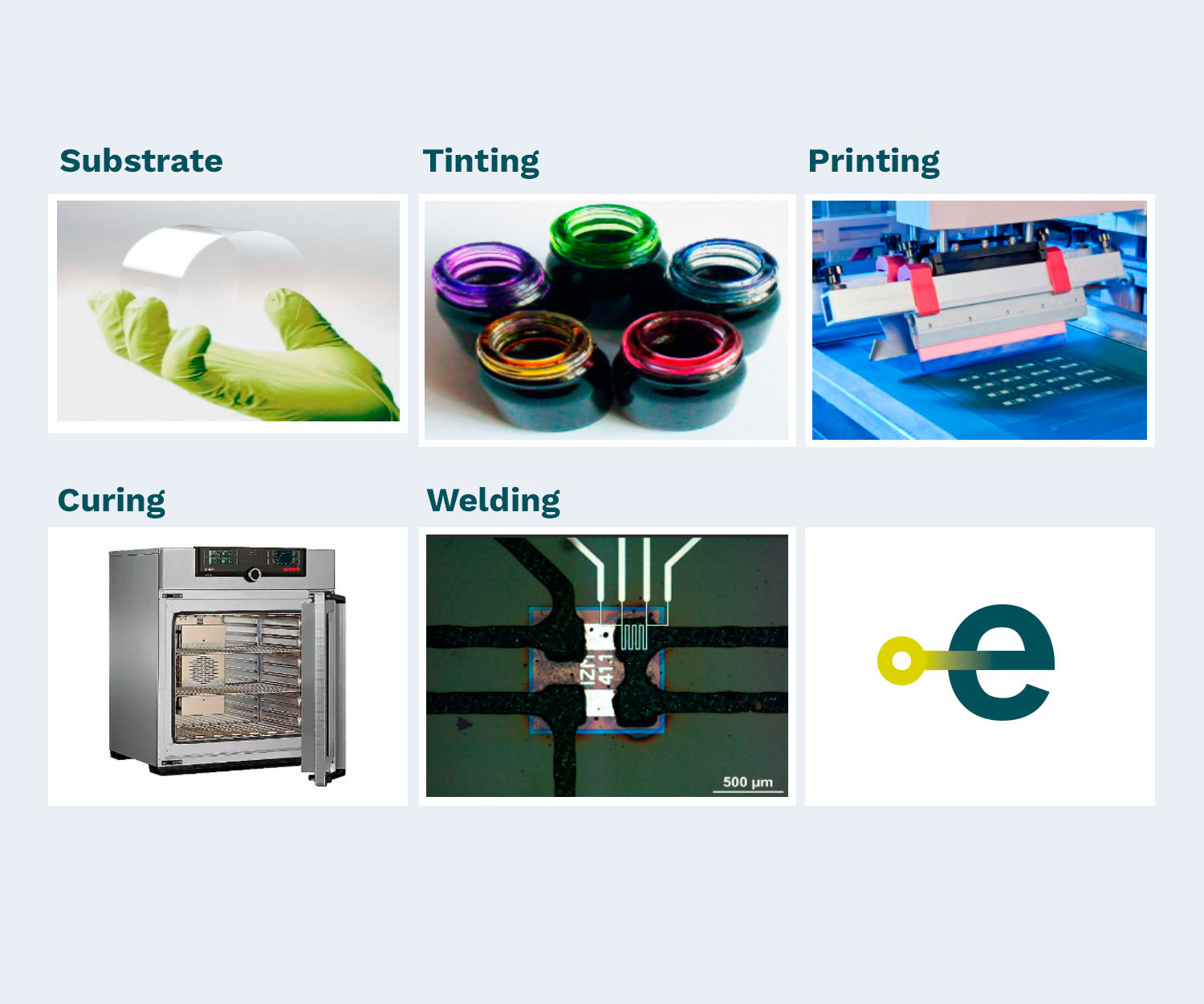
Applications
Flexible circuits have a multitude of applications in today’s markets:
Printed electronics in important industrial sectors
Monitoring for preventive care
Wellness and health purposes
Biosensors
OLED for light therapy
Smart ampoules
Displays as decorative applications
OLED luminaires
Detection and signaling for household appliances
Tactile and functional surfaces
Low cost and consumption displays for price tags
Smart tickets and labels
Smart packaging combining sensor systems
Energy collection and storage
Printed and hybrid NFC and RFID tags
Gadgets
NFC, RFID antennas
Geolocation, GPS (hybrid electronics)
Motion monitoring
Printed light
ECG, respiration, temperature monitoring
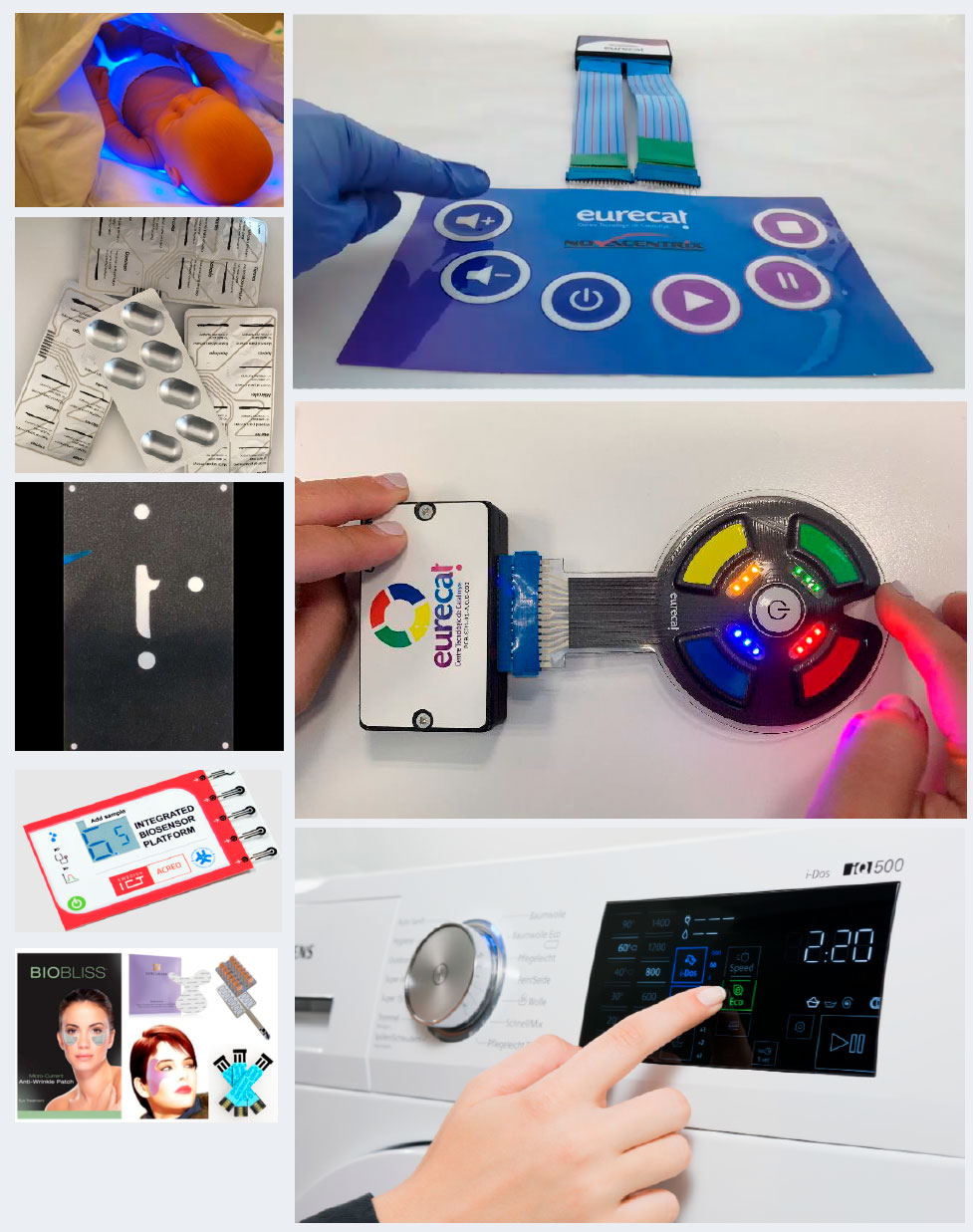